Der Einsatz digitaler Zwillinge spielt eine zentrale Rolle für eine erfolgreiche digitale Transformation von Produktionsunternehmen im Sinne von Industrie 4.0. Zwei Beispiele sollen illustrieren, wie die virtuellen Doppelgänger effizientere Wartungsprozesse im Shopfloor und zukunftsfähige Geschäftsmodelle ermöglichen.
Was ist ein digitaler Zwilling?
Auch wenn es keine allgemeingültige Definition des Begriffs gibt, umschreibt ein digitaler Zwilling die virtuelle Abbildung eines real existierenden Objekts. Er basiert auf Daten und Informationen, die an einer zentralen Stelle zusammenlaufen, und bildet so den gesamten Lebenszyklus eines Produkts ab – von Planung und Design über Fertigung und Transport bis hin zur operativen Phase, in der das Asset zur Anwendung kommt. Damit sich dieses lückenlose Gesamtbild ergibt, müssen die Informationen verschiedener Systeme integriert und mit Live-Daten angereichert werden. Modernes Equipment verfügt standardmäßig über entsprechende Technik, alte Anlagen lassen sich im Zuge von Retrofitting entsprechend nachrüsten.
Digitaler Zwilling – Beispiel 1: Predictive Maintenance im eigenen Shopfloor
Ein Fertigungsunternehmen hat mit verschleißbedingten Ausfällen seiner in der Produktion eingesetzten Maschinen zu kämpfen. Die ungeplanten Stopps der Anlage verursachen erhebliche Verzögerungen und kosten bares Geld. Da die Störungen ohne den Einsatz eines digitalen Zwillings kein klares Muster erkennen lassen, setzt man zunächst auf Preventive Maintenance, also dem Austausch bestimmter Teile in einem festgelegten Turnus. Der Nachteil: Bei diesem Konzept werden mitunter auch Teile ausgetauscht, die noch einwandfrei funktionieren. Das vermindert zwar die Ausfälle, ist aber trotzdem ein ineffizienter Einsatz von Ressourcen.
Deswegen entschließen sich die Verantwortlichen, die Maschinen im Shopfloor digital nachzurüsten. So werden nicht nur die verbauten Einzelteile der Anlage dokumentiert und digital gespeichert, sondern auch die wichtigsten Produktionsparameter wie Temperatur, Druck, Materialbeschaffenheit, etc. durch Sensoren erhoben. Hinterlegt werden alle diese Informationen in der SAP Asset Central Foundation. Mit diesem digitalen Zwilling kann das zuständige Fachpersonal jetzt bereits im Voraus erkennen, dass ein bestimmtes Bauteil bald verschlissen ist und einen Produktionsstopp erzwingen wird. Entsprechend wird es im Rahmen einer geplanten Wartungspause dann rechtzeitig ausgetauscht.
Darüber hinaus bildet der digitale Zwilling auch die Grundlage für weiterführende Datenanalysen. Dabei zeigt sich: Ein bestimmtes Kugellager ist besonders anfällig für Verschleiß und musste in den vergangenen 24 Monaten bereits vier Mal getauscht werden. Gehäuft hatten sich die Ausfälle, nachdem ein günstigeres Modell eines anderen Herstellers verbaut wurde. Diese Erkenntnis fließt jetzt im Sinne von „Data to Action“ zurück in das SAP-basierte ERP-System, das den Einkauf anweist, das qualitativ anscheinend minderwertige Bauteil nicht mehr zu bestellen.
Digitaler Zwilling und das Management der Zukunft
Digitaler Zwilling – Beispiel 2: Neue, digitale Servicemodelle
Ein Hersteller von Härtungsöfen möchte seine Geschäftsmodelle um neue, digitale Services erweitern. Diese sollen von erweiterten Wartungsleistungen bis hin zu „Härtung-as-a-Service“ reichen – ein Modell, bei dem der Kunde statt der ausgelieferten Produkte lediglich deren Leistung und Betrieb im Rahmen einer nutzungsbasierten Abrechnung bezahlt.
Voraussetzung für diese neuen Angebote ist die Bereitstellung entsprechender Daten. Einige grundlegende Informationen wie Zeichnungen, Schaltpläne etc. muss der Hersteller als „abgespeckten digitalen Zwilling“ ohnehin pflichtgemäß an den Kunden weitergeben. Das gilt jedoch nicht für kontinuierlich und in Echtzeit erhobene Zahlen, die am Produkt über Sensoren erfasst werden und beispielsweise Auskunft über Temperaturschwankungen oder den Zustand der Brennkammer geben. Auch andere weiterführende Informationen wie animierte CAD-Zeichnungen oder Services für Augmented Reality (AR) gehören nicht zu diesem Standard-Paket.
Wer nach dem Kauf also ein komplettes Bild seines Ofens haben möchte, bestellt beim Hersteller ein entsprechendes Zusatzpaket. Dieser kann mit der Unterstützung von IT-Spezialisten wie Syntax beispielsweise ein Master Date Package auf Basis von des SAP Asset Intelligent Network (AIN) anbieten, das den standardmäßig ausgelieferten digitalen Zwilling erweitert. Bucht der Endkunde dieses Angebot, profitiert er dann beispielsweise von AR-Kapazitäten, die die Werker vor Ort bei fälligen Wartungsarbeiten Schritt für Schritt digital anleiten. Das spart den externen Servicetechniker, Zeit und Geld.
Alle Services für den digitalen Zwilling über eine Plattform
Idealerweise stellt der IT-Dienstleister Hersteller und Kunden darüber hinaus eine zentrale IIoT-Plattform zur Verfügung. Lösungen wie Synsights dienen als Speicherort und ermöglichen neben einer gemeinsamen Sicht auf den digitalen Zwilling auch eine schnelle und unkomplizierte Kommunikation. So kann der Endkunde bei einem Problem beispielsweise statt einer Mail direkt über die Plattform eine Anfrage stellen, deren Details der Hersteller gleich mit dem betreffenden Produkt in Bezug setzen kann. In einem nächsten Schritt lassen sich dann über eine entsprechende Anwendung sogar Ersatzteile direkt aus dem System heraus bestellen, ohne vorher auf einen Shop zugreifen zu müssen. So verbessert der digitale Zwilling das Serviceerlebnis – und stärkt die Kundenbindung.
Mit Syntax alle Vorteile des digitalen Zwillings nutzen
Der digitale Zwilling ist vielen Verantwortlichen in der Produktion ein Begriff, denn er bringt zahlreiche Vorteile – von der prädiktiven Wartung bis hin zu neuen Geschäftsmodellen, bei denen der Kunde nur noch für den Betrieb bezahlt. Doch nicht alles, was in einer digitalen Fabrik möglich ist, ist auch immer sinnvoll. Deswegen sollten sich Fertigungsunternehmen auf dem Weg zu Industrie 4.0 einen versierten Partner wie Syntax an die Seite holen. Wir erstellen gemeinsam mit Ihnen ein maßgeschneidertes Leistungspaket, das Ihren individuellen Anforderungen am besten entspricht – und runden unser Angebot durch eigene Lösungen wie die IIoT-Plattform Synsights ab.
mit unserem Experten!
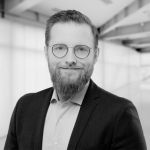