IIoT zielgerichtet einsetzen
Die Vernetzung von Fertigungsanlagen ist Grundvoraussetzungen für das Erheben von Daten – und damit auch für eine funktionierende Digitalisierung in der Produktion. Es gilt, alle analogen Vorgänge im Shopfloor digital zu erfassen, abzubilden, auszuwerten und miteinander in Beziehung zu setzen. Über nachgerüstete Sensoren lassen sich die Informationen wie Materialqualität, Temperatur, Druck oder Ähnliches in Echtzeit erheben. Weitergeleitet und ausgetauscht werden diese Daten dann innerhalb eines Industrial IoT (IIoT)-Netzwerks, in dem alle Teilnehmer miteinander kommunizieren können. Dies ermöglicht moderne Verfahren wie beispielsweise Predictive Maintenance und Predictive Quality.
„Viel hilft viel“? Nicht unbedingt. Denn nicht alle Parameter, die im Rahmen der Produktionssteuerung erhoben werden können, bringen für die Prozessoptimierung auch einen echten Vorteil. Damit Produktivität und Effizienzgewinne nicht gleich wieder verpuffen, ist Verhältnismäßigkeit gefragt. Wer seine Maschinen mit Augenmaß nachrüsten und seine IIoT-Umgebung zielführend aufbauen möchte, sollte sich am besten einen erfahrenen Partner an die Seite holen, der sich sowohl in der IT als auch der OT (Operational Technology) auskennt.
Daten und Erfahrung kombinieren
Egal, wie viele Daten man erhebt und wie oft man den Algorithmus anpasst: Digitale Lösungen werden niemals die jahrelange Erfahrung der Werker an der Linie ersetzen – und das sollen sie auch nicht. Im Gegenteil: Digitalisierung in der Produktion bedeutet, dass IT-gestützte Lösungen und menschliche Kollegen zusammenarbeiten. Ziel ist, wertvolles Fachwissen in die neuen Prozesse mit einfließen zu lassen. Das funktioniert beispielsweise über mobile Endgeräte, die als Mensch-Maschine-Schnittstelle (HMI) dienen und mit denen die Werker Feedback ans System geben, um Abläufe anzupassen.
Dazu ein Beispiel einer solchen Zusammenarbeit in einer Industrie 4.0-Umgebung: Ein Mitarbeiter arbeitet seit über 20 Jahren an denselben Maschinen und weiß: Wenn die Anlage ein bestimmtes Geräusch von sich gibt, dauert es nicht mehr lange, bis sie sich aus Sicherheitsgründen selbst abschaltet. Kombiniert man dieses Wissen mit den Sensordaten, lässt sich das zeitliche Auftreten des Geräuschs in Verbindung mit konkreten Produktionsparametern setzen, die zu diesen Zeitpunkten erhoben wurden. Das kann dazu beitragen, die Fehlerquelle schnell zu identifizieren und sie dauerhaft zu beheben.
Ganzheitliches Konzept entlang der gesamten Supply Chain
Der Shopfloor ist das Herzstück eines Fertigungsunternehmens, hier findet an den Linien ein Großteil der Wertschöpfung statt. Doch Digitalisierung in der Produktion geht über die Fabrikhalle hinaus. Um das volle Potenzial dieser Transformation ausschöpfen zu können, müssen IT-Verantwortliche ein gesamtheitliches Konzept entwickeln und umsetzen, das alle Teilprozesse entlang der Wertschöpfungskette umfasst – vom Einkauf über die eigentliche Herstellung bis hin zu interner Logistik, Auslieferung und Aftersales Services.
Funktioniert dieses ganzheitliche Konzept, reagiert das zugrunde liegende ERP-System idealerweise dynamisch auf Änderungen oder Probleme. Ein Beispiel: Das MES, also das System für die Produktionssteuerung einer Maschine, meldet eine schlechte Produktqualität und kann diesen Umstand konkret mit einem scheinbar minderwertigen Rohstoff in Verbindung bringen. Entsprechend schickt der Werker an der Linie auf digitalem Weg eine direkte Anweisung an den Einkauf, den Rohstoff künftig von einem anderen Anbieter zu beziehen.
Change Management
Bei Industrie 4.0- und IIoT-Projekten gilt: Ohne IT funktioniert es nicht – allein mit IT aber ebenso wenig. Um sicherzustellen, dass die Umstellungen, die eine Digitalisierung in der Produktion mit sich bringt, auch Früchte tragen, müssen alle Beteiligten mit an Bord sein. Das ist nicht immer einfach, denn Digitalisierung in der Produktion bedeutet auch, gewohnte Prozesse anzupassen oder sogar komplett mit ihnen zu brechen. Wer seit vielen Jahren Laufzettel ausdruckt und jetzt papierlos auf ein Tablet oder Smartphone umsteigen soll, sträubt sich mitunter dagegen.
Deswegen machen gute Manager „von der Transformation betroffene Mitarbeiter“ zu „an der Transformation beteiligte Kollegen“. Sie nehmen Bedenken ernst, zeigen die Vorteile digitaler Produktionsprozesse auf und bauen so Vorbehalte ab. Denn nur, wenn die gesamte Belegschaft an einem Strang zieht, wird das Projekt gelingen.
Digitales Mindset etablieren
Dieser letzte Punkt hängt unmittelbar vom vorher erwähnten Change Management ab. Denn die Digitalisierung in der Produktion ist nur dann dauerhaft erfolgreich, wenn sie auch den Aufbau einer „digitalen Belegschaft“ umfasst. Damit sind keine Bots gemeint, sondern eine motivierte Mitarbeiterschaft, die sämtliche unternehmensinterne Abläufe automatisch digital mitdenkt und die Führungskräfte durch Feedback bei der Planung und Implementierung neuer Produktionsprozesse unterstützt.
Ein digitaler Shopfloor ist Ausgangspunkt für mehr Produktivität und moderner, zukunftsfähiger Geschäftsmodelle, doch die beste Technologie nutzt nichts, wenn die Belegschaft noch in alten Mustern denkt. Deswegen ist die Digitalisierung in der Produktion Chefsache: Das Top-Management muss die digitale Transformation anführen, nachhaltig vorantreiben und mit den Mitarbeitern regelmäßig über Digitalisierung sprechen – die Verantwortlichen werden begeistert feststellen, dass es eine ganze Flut an guten, neuen Ideen gibt.
Aus Herausforderungen Chancen machen – mit dem richtigen Partner
Die Digitalisierung in der Produktion ist ohne Frage ein Mammutprojekt, das weit über eine bloße Nachrüstung und Vernetzung von Fertigungsanlagen hinausgeht. Sollen am Ende zukunftsfähige Umsatzmodelle stehen, müssen alle Prozesse der unternehmensinternen Wertschöpfungskette genau durchleuchtet, angepasst oder sogar komplett verworfen werden. Und die Belegschaft muss fraglos mit an Bord.
Versierte Partner wie Syntax kennen sich nicht nur mit der erforderlichen Technologie bestens aus, sondern haben auch Erfahrung darin, Mitarbeiter aktiv in die digitale Transformation einzubeziehen und so Vorbehalte abzubauen. Sprechen Sie mit uns – wir unterstützen Sie bei Planung und Umsetzung, damit Sie mit Ihrem Industrie 4.0-Projekt das volle Potenzial ausschöpfen!
mit unserem Experten!
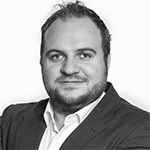